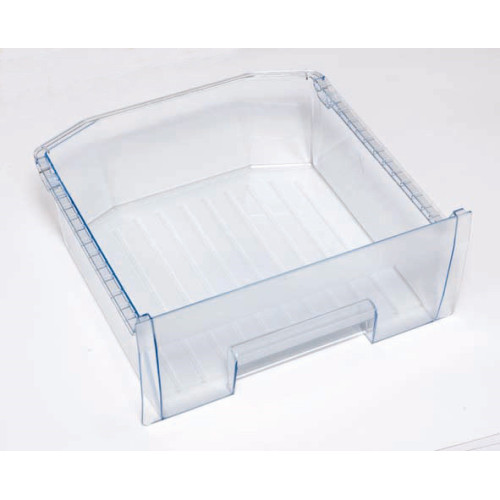
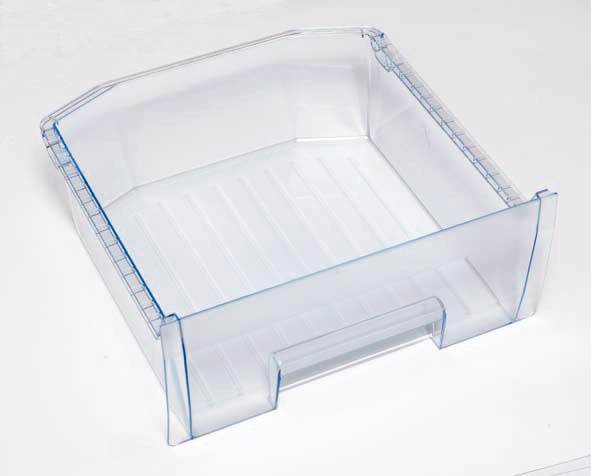
Payment Type:L/C,T/T,D/P,D/A,Paypal
Incoterm:FOB,CFR,CIF,FCA,EXW,FAS,CPT,CIP,DEQ,DDP,DES,DAF,Express Delivery,DDU
Min. Order:1000 Set/Sets
Transportation:Ocean,Air,Land,Express
Port:Ningbo,Shanghai
$10000≥1000Set/Sets
Model No.: CT-10875
Brand: Ceeto
Place Of Origin: China
Forming Method: Plastic Injection Mould
Product Material: Plastic
Product: Household Product
Shaping Mode: Injection Mould
Surface Finish Process: Polishing
Mould Cavity: Single Cavity
Plastic Material: ABS
Process Combination Type: Single-Process Mode
Application: Household Appliances
Runner: Hot Runner
Design Software: UG
Installation: Fixed
Certification: ISO
Standard: HASCO
Customized: Customized
Packaging: Wooden box
Productivity: 500000shots/mold life
Transportation: Ocean,Air,Land,Express
Place of Origin: China
Supply Ability: 5sets/month
Certificate: ISO
HS Code: 8480790090
Port: Ningbo,Shanghai
Payment Type: L/C,T/T,D/P,D/A,Paypal
Incoterm: FOB,CFR,CIF,FCA,EXW,FAS,CPT,CIP,DEQ,DDP,DES,DAF,Express Delivery,DDU
Injection Mould for Refrigerator Drawer
How to design a good core-pulling mechanism structure in the Refrigerator Drawer Plastic Injection Mold?
Please look at A, B highlighted in arrow area, which will be talked in critical points. As we know that these two areas are very special, Slider core-pulling design must be used in both side areas in the Refrigerator Drawer Plastic Injection Mold design specification. However, you may notice the inward slot highlighted in circle in picture a), it`s named handle in this plastic drawer. You may see it in details in section like picture c). In terms of Refrigerator Drawer mold structure, this groove or slot must use an upward core-pulling slider in order to release the mold. but since there has been a large core-pulling slider on this side so only the core-pulling angle lifter structure in the secondary core-pulling slider can be used. Please look at picture d) that there are two inward clips, clips could not be demoulded normally, sliders must be used as well.
1- Spring 2- Spring Guide Pillar 3-Hydraulic cylinder
As can be seen from Refrigerator Drawer Plastic Injection Mold structure diagram, there are 8 important leaders in the angle lifter structure of the secondary core pulling structure: Spring 1, spring guide pillar 2, delay block 10, Angle lifer 11, Angle lifter limit block 12, Angle lifter seat 13, Pressing plate 15, Guide sleeve 16. The angle lifter block 12 not only plays the role of stroke limit, but also plays a large stop role on the angle lifter. Delay block 10 mainly controls the delay motion of the angle lifter. Spring 1 is the source of angle lifter moving.
The principle of action of the entire organization: After opening the mold, the slide block 14 starts to move backward under the drive of the hydraulic cylinder 3, the slant 11 moves up the slider under the action of the delay block 10 and the spring 1, and begins to pull out the inverted buckle of the handle, and when the slider 14 moves backward to l distance, Limit block 12 begins to limit the angle lifter. At this time, the angle lifter has also moved upward into a distance of L1, completely out of the reverse buckle of the product part, and the slide block continues to move, thus driving the whole angle lifter structure to complete all the core pulling. When the slider is reset, the straight face of the delay block 10 is tightly on the slot of angle lifter, thus forcing the angle lifter to reset.
4- Guide Pillar 5,16- Guide Bushing 7-Cavity sliders 8-Pull hook 9-Limit pulling rod 10- Delay Block 11- Angle lifter 12- Angle lifter limit block 13- Angle lifter seat 14- Slider 15- Pressure Pad
We talk about cavity slider no.7 in the picture. This design for cavity slider of Refrigerator Drawer Plastic Injection Mold is very simple and as well as applicative, the slider 7 is driven by spring such as the driven by spring 6 and pull hook 8, guiding mechanism is guide pillar 4 and guide bushing 5, the travel limit mechanism is the limit rod 9, when the slider is reset, it is directly pressed back by the parting surface. This is very good design for Refrigerator Drawer Plastic Injection Mold and also very important for a plastic mold design to learn.
Ceeto company has many years experience in design the Refrigerator Drawer Plastic Injection Mold, if you have any questions, please leave a message for us, we shall be very glad to give you response soon.
Requested high polishing or mirror polishing refrigerator drawer plastic mould, production capacity for moulds is about 400 sets/year. Detailed Mould Description, mould design software: UG, Pro-E, Solidwork , mould cavity is Single cavity, mould base can be LKM, DME, HASCO, PUNCH etc., mould cavity and core steel is 2738 or P20 ( HRC 38-42 ), type of gate is hot runner ( Direct gate ), and hot runner name brand is Mold-master. Cycle time: 35', and mould making Lead time is 60 days from mould design approval to the first shot, ejection system: ejectors pins.
Our core competition
Machining process
High-speed EDM milling
Gun drilling machining
FAQ:
Q1: How do you control quality?
We strictly following product 2D drawing to use calipers and CMM measuring equipment to check critical dimensions of plastic mould or plastic sample parts, and write down dimension reports for each mould tryouts T0, T1, T2 ...
Q2: How long will you take for mould design?
Regarding fridge drawer plastic mould, we will start DFM and submit DFM report to customer when we receive product 2D and 3D model, we will start mould design when we get approval for DFM, it will take 1 week time to complete rough mould design and submit it to customer for review, we may improve mould design and complete all components including cooling after receiving customer's feedback, 2 weeks more will be added until we have got approval of mould design from customer.
Q3: Are you doing dry cycle for the mould before shipping?
Yes, we have been always implementing dry cycle before shipping, the empty cycle is about 2000 times. It will check mould function to avoid any damage happen when mould is shipped to the customer site.