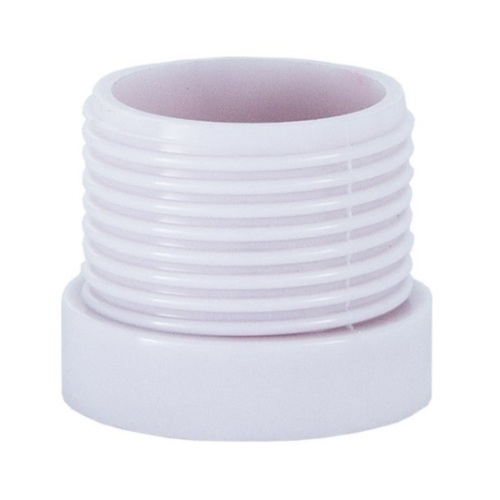
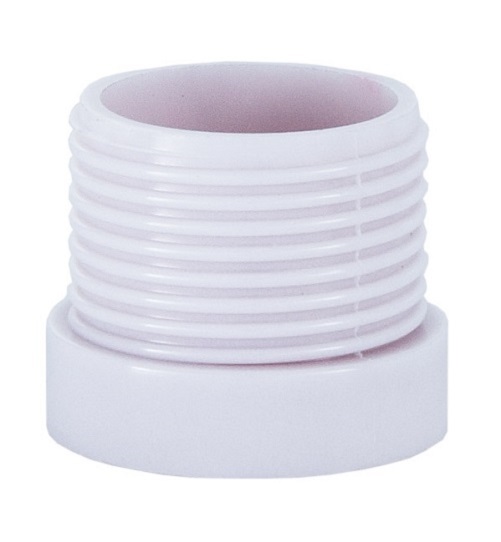
Payment Type:L/C,T/T,D/P,D/A,Paypal
Incoterm:FOB,CFR,CIF,FCA,CPT,EXW,FAS,CIP,DEQ,DDP,DES,DAF,Express Delivery,DDU
Min. Order:1 Piece/Pieces
Transportation:Ocean,Land,Air,Express
Port:Ningbo,Shanghai,Shenzhen
$1000-50000 /Piece/Pieces
Model No.: CT-10932
Brand: Ceeto
Place Of Origin: China
Forming Method: Plastic Injection Mould
Product Material: Plastic
Product: Household Product
Some Parts Can Be Desgined Multi Cavity Mould: Mould Design Can Be Pro-E As Well
Packaging: Wooden box
Productivity: 500000shots/mold life- 1000000
Transportation: Ocean,Land,Air,Express
Place of Origin: China
Supply Ability: 30sets/month
Certificate: ISO
HS Code: 8480790090
Port: Ningbo,Shanghai,Shenzhen
Payment Type: L/C,T/T,D/P,D/A,Paypal
Incoterm: FOB,CFR,CIF,FCA,CPT,EXW,FAS,CIP,DEQ,DDP,DES,DAF,Express Delivery,DDU
Screw Thread Cap Plastic Injection Mold
How to make High Quality Screw Thread Cap Plastic Injection Mold? Automatic unscrew mechanism is a very common and important structural type in plastic mold.This kind of Cap product is round shape and not big, so mold outside dimension is not big neither, so it belongs to middle size or small size plastic injection mold. Therefore, the products with thread screw are classified as caps products. The plastic material using for caps products are much more stronger such as ABS, PBT, PA66, PEI etc. Due to the character of small deformation, it`s not a good way to demould the caps from plastic injection mold by force. So, use of Automatic Thread Mechanism is the safest way to unscrew this kind of cap plastic injection mold.
Sometimes, depending on the profile, distance and depth of the thread, if the thread spacing is small, there is no space between the two screws, and the tooth shape is thin and sharp, even if the product is made of pp plastic material. Also make up for forced release, must use automatic thread. If the thread spacing is large, there is a distance between the two screw teeth, and there is a large arc at the cusp of the tooth shape, even if the depth reaches 1.5 mm, the hard wood material can also be used for forced demoulding. There is no need to unscrew automatically.
The automatic unscrew mechanism is classified according to the power transmission mode, and there are three types as follows.
A) Motor drive. The motor has a motor and a hydraulic motor. Because the rotating speed of the motor is too fast and the action is not stable, the motor is less in use, and the hydraulic motor is relatively slow in rotating speed, stable in operation, safe and reliable, and is therefore widely used. The use of a motor-driven mould with almost 95% of the use of a hydraulic motor, with the use of a hydraulic motor, must have two additional accessories, i.e., sprockets and chains, which are combined with each other. The motor, the chain wheel and the three most important combination parts of the chain are not indispensable, and the motor transmission can be realized.
B) Thread drive. The screw drive uses a multi-screw rod and a matching spiral sleeve, an important combination of components to drive the gear rotation. The die structure of thread transmission is the simplest among all the automatic screw removal mechanisms, and the die structure is greatly simplified by thread transmission. Screw rod and spiral sleeve are imported German hasco standard parts.
C) Hydraulic cylinder rack drive. This structure is mainly driven by hydraulic cylinder rack, rack redrive gear to achieve work. The disadvantage of this structure is that the hydraulic cylinder and rack will take up a lot of space in the mould, which makes the overall shape of the mould appear to be some huge, which brings great inconvenience to the lifting and transportation of the mold. But this kind of structure has good stability and reliability, so it is also widely used, and it is one of the most widely used structures.
Above mentioned Automatic Thread Mechanism structures are very common. We may see a classic bottle cap Plastic Injection Mold design structure as follows.
This cap plastic mold is two cavity mold,totally having 11 plates. This is very good mold design for thread screw cap plastic mold. Looking at the cavity side of this mold, it has two plates as follows. plate 11 and A plate No.10, The core side of mold have 8 layers and 9 plates and two pressure plates. Stripper plate 9 is used to push out the cap plastic part and fixing inserts No.13 of stripper plate. Support plate No.8 is used to fix and support stripper plate inserts No.13, it`s connected and fixed through a screw pin. Core fixing plate No.7 is used to fix core insert No. 14, core support plate No. 6 is used to fix and support core No.14. This Cap mold gear is hidden in the gear reposition plate No.5. Screw bushing No. 31 is used to control screw core No.16 up and down moving, This mold has two screw bushings to be fixed in the screw bushing fixing plate No.4. The location busing is specially used for precise guidance and location of bottom of screw core No.16, which is fixed in the location bushing fixing plate No.3. Two A plate No.10 is specially used to place chain wheel No.20 and chain No.28 in order to guarantee enough satefy space for chain and chain wheel moving. Cooling Insert Fixing plate No.19 is used to fix cooling insert No.18, which is fixed on plate 1 by several screws and to keep it stationary state.
This Cap plastic Mold is Automatic Thread removal Mechanism of hydraulic Transmission. The way out of the thread is that the thread core retreats synchronously in the rotation. When the thread core completely exits and stops, the product will drop freely at the end of the product when the screw core is pulled out of the product by the push plate.
The detailed moving principle is as follows. When the Cap Plastic Mold is open, main parting surface PL1 is firstly apart, the plastic cap parts stays in core side, and after mold open action is stopped, hydraulic motor is starting to work, at the same time, chain wheel No.27 drive chain No.28 moving, chain No.28 drive chain wheel No.20 and drive spiale No.22 with gear No.23 for moving. Under driven of gear No.23, two chain wheels No.15 drive screw core No.16 is rotated in reverse way of screw tooth, at the same time, with the help of screw bushing No.31, two screw cores are compressed under way at the same time rotation and product in screw part can be demoulded, when it moved in L direction, gear No.15 starts to touch limit switch No.34, hydraulic motor No.25 stop to rotate, chain wheel, chain and gear and other rotate components all stop working. At this time, screw core No.16 is apart from the legth of product, but molding is on the core No.14 for the surround clips features, product is still fixed on core No.14, so injection machine push the stripper plate fixing plate No.29 and two stripper rods No.30 to eject forward. stripper rod No.30 is also pushing two stripper plates No.8 and No.9 at the same time to eject, finally cap product can be ejected from core No.14 and automatic drop down, the automatic demoulding process is finished.
In order to meet big mass production requirement, we may design the plastic threaded cap mould 10 cavity with hot runner system, mould cavity is arranged in double rows. Descrew with gear rack rotating mechanism. When Plastic Threaded End Cap Injection Mould is open when injection, parting surface will be firstly parted, and the product stay on the core side, we have a group of mould designers with professional skills to design the mould.
Ceeto company has a group of skilled tooling engineers who are able to support you to solve any technical doubts and difficulities, our advantages:
We do wish you to visit our company and start to make business, we do hope that we may receive your RFQ very soon, if you have any technical questions, please don't hesitate to let us know, thank you very much.